Automation in the construction industry continues to grow while becoming more feasible with advanced sensor technology and enhanced computational power. Development of assistance systems that control the hydraulic actuators of the deployed machines facilitate the autonomous execution of repetitive tasks.
The telescopic handler, or telehandler, is a hydraulically actuated construction vehicle with an extendable telescopic arm. With the lifting motion of the arm as well as tilting of its bucket or fork attachment, this results in three degrees of freedom for the work functionality, which is actuated by hydraulic cylinders. Driving the mobile machine is achieved by means of its hydro-mechanical powertrain. Hydraulic pumps are propelled by an engine and deliver fluid to the telescopic handler’s hydraulic sections, which cause the desired movement through pressure changes.
The objective of the research project is to develop a velocity control scheme for the hydraulic cylinders of telescopic handlers as a foundation for assistance systems and automation functions that increase productivity and safety. Thus, a detailed dynamic model is derived, which enables the design of a model-based state feedback controller. Validation of the resulting digital twin and performance analysis of the designed control concepts as well as the developed functions are conducted by means of measurements with telehandlers of the type T55-7s and T46-7s.
An effective and robust velocity controller for the hydraulic actuators combines the application of methods so that the cylinder velocities follow specified trajectories. Inverting the model yields an efficient feed-forward controller, while linear control algorithms for the state feedback, such as LQR, require a linearization of the nonlinear system dynamics. Estimated system states are considered in the feedback component of the controller as well as for the generation of optimal trajectories.
The implementation of a function is realized by a corresponding trajectory generation, which passes reference time signals to the controller while considering the system constraints. For example, a motion of the end effector to a specified end position or a planar movement can be implemented in this way. Further functions are the limitation of the load torque, which prevents the machine from tipping over, and a playback functionality repeating taught-in motions.
- Liebherr-Werk Telfs GmbH
Project partner for the research project - Telescopic Handler by Liebherr
Considered system in the research project
Contact
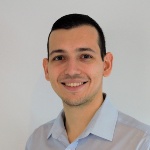
Christos Parlapanis
M.Sc.Research Assistant